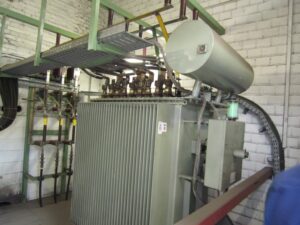
Ds-Oel step transformer 850kVA
mainly consists of: Ds-Oel step transformer 850kVA No. 8926048 Rated voltage: 20,000 +/- 5% // 180 – 780 V / 8 steps Rated current: 24.5
mainly consists of: Ds-Oel step transformer 850kVA No. 8926048 Rated voltage: 20,000 +/- 5% // 180 – 780 V / 8 steps Rated current: 24.5
Mainly consists of: DISAMATIC Model 2110 Mk3 Allen Bradley PLC Upgraded VDU Automatic Core Setter Automatic Spray System 12 Meter AMC Technical Data: Mold Dimensions:
Planetary gearbox RSD 140V for up to 30 ton pouring ladle Nominal torque: 32,000 Nm T-max.: 51,600 I-ratio: 203 Shaft journal diameter: 140 mm
Mainly consists of: 2 mobile charging vehicels with load cells 2 Furnace bodies, each with a tilting chair; furnace lid and ring exhaust; 2 hydraulic
Mainly consists of: Specifications Work Envelope 20" dia x 7.8" H (500 mm dia x 200 mm H) Max Total Weight (Part + Fixture and
Flask size: LxBxH: 1350 x 900 x 400 / 400 mm Mainly consists of: 1 Moulding machine 5 Cope & 5 Drag Flasks 1 set
Automatic Core Shooter for Cold-Process 20 ltr designed for horizontal & vertically parted core boxes Vacuum-Clamping plates Max. Core Box Dimensions: Horizontal core box Width/Depth/Height=
Mainly consists of: Portable spectrometer for metal analysis of iron, aluminum, nickel, and steel Housing Screen Storage compartment Probe holder Trolley Probe Argon cylinder holder
Mainly consists of: -2 pc. MF furnace bodies (18 tons & 12 tons) -Tilting chair with hydraulic cylinder -Furnace lid with exhaust system -1pc. 7.000
Mainly consists of: Conveyor belt with casting molds Air cooling molds Mold preheating station with gas burner Control cabinet with frequency converter (speed setting) Transfer